A lathe is a machine tool that performs various operations by rotating a workpiece about an axis of rotation. These operations include cutting, sanding, knurling, drilling, deformation, facing, and turning. Lathes are essential in shaping materials into cylindrical, conical, or complex shapes with symmetrical precision. The core components of a lathe include the bed, headstock, tailstock, carriage, and tool post. The bed serves as the main frame, providing structural integrity. The headstock houses the motor, which drives the spindle to rotate the workpiece. The tailstock can be adjusted to support the other end of the workpiece. The carriage, which moves along the bed, carries the tool post where the cutting tool is mounted. Lathes are crucial in providing mechanical and electrical services across various industries.
How It Works?
A lathe operates by securely holding the workpiece in a chuck or between centers, then rotating it at high speeds. The cutting tool, mounted on the tool post, is moved into the rotating workpiece to remove material and shape it as desired. The tool post can be adjusted to move the cutting tool along different axes, allowing for precise control over the machining process. Lathes can be operated manually, where the operator adjusts the tool’s position and feeds, or by computer numerical control (CNC), which automates these movements based on pre-programmed instructions. CNC lathes use servomechanisms to precisely control the tool’s movements, enabling the production of complex shapes with high precision and consistency.
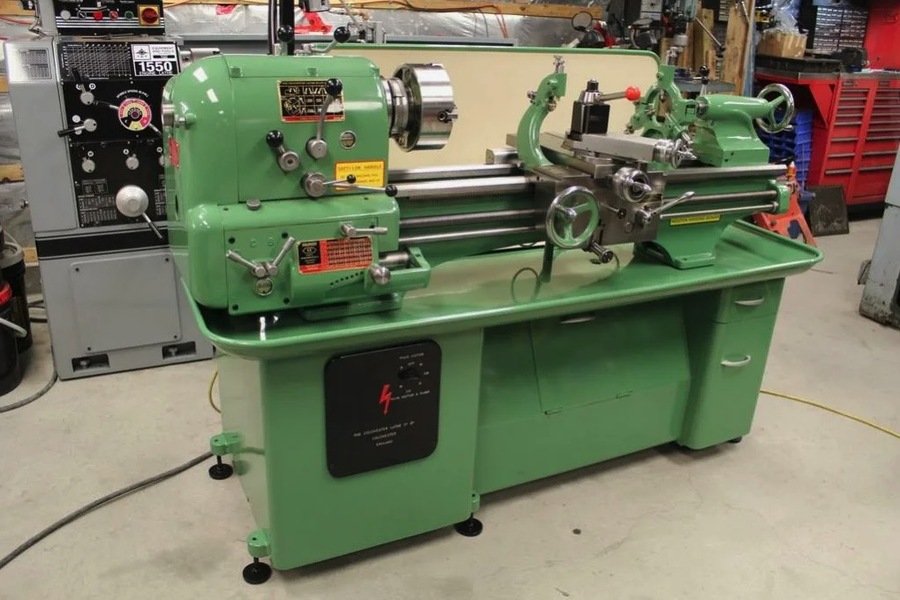
Work Performed on a Lathe
Lathes perform a variety of tasks, including:
– Turning: Shaping the exterior of a workpiece to achieve a desired diameter and surface finish.
– Facing: Creating a flat surface at the end of a workpiece by cutting perpendicularly to the axis of rotation.
– Parting: Cutting off a part of the workpiece.
– Drilling: Creating holes in the workpiece by advancing a drill bit mounted on the tailstock into the rotating workpiece.
– Knurling: Impressing a pattern onto the surface of the workpiece for grip.
– Threading: Cutting threads on the exterior or interior of a workpiece to create screws and bolts.
History of the Lathe
Ancient Beginnings
The earliest evidence of lathes dates back to Ancient Egypt around 1300 BC. These early lathes were simple, manually operated devices used to shape wood and soft materials. The basic design included a horizontal beam to hold the workpiece and a bow to turn it while a tool was held against the workpiece to shape it.
Evidence of lathes has also been found in the Mycenaean civilization of the 13th or 14th century BC, indicating the widespread recognition of their utility in shaping materials. These early machines laid the groundwork for future advancements in lathe technology.
Etruscan and Chinese Innovations
In the 6th century BC, clear evidence of machine-made artifacts was discovered, such as fragments of a wooden bowl in an Etruscan tomb in northern Italy. This indicates that the Etruscans had developed the technology to produce precise and symmetrical objects using lathes.
During the Warring States period in China (around 400 BC), lathes were used on an industrial scale to sharpen tools and weapons. This reflects the advanced state of Chinese technology and their ability to mass-produce essential items for warfare and daily life.
Development Through the Ages
The first known depiction of a lathe dates back to the 3rd century BC in Ancient Egypt, illustrating the machine’s basic principles and design. This depiction underscores the significance of lathes in ancient craftsmanship.
In 1717, Andrei Konstantinovich Nartov, a court turner for Peter the Great, invented a screw-cutting lathe. This innovation allowed for precise threading of screws, significantly advancing the capabilities of lathes and improving their versatility.
Around 1751, Jacques de Vaucanson invented the first fully documented all-metal lathe. This design incorporated significant improvements in stability and precision, enabling the machining of harder materials and laying the foundation for modern metalworking lathes.
Industrial Revolution and Modern Advances
An important early lathe in Britain was the horizontal boring machine installed in 1772 at the Royal Arsenal. This machine allowed for the precise boring of cannon barrels, improving the accuracy and reliability of artillery, and marking a significant step in industrial manufacturing capabilities.
Between the late 19th and mid-20th centuries, individual electric motors replaced linear shafts as the power source for each machine tool, increasing efficiency and flexibility. This shift allowed for more compact and versatile machine designs, making lathes more accessible and easier to use.
From the 1950s onward, the integration of servomechanisms and computers led to the development of CNC lathes. These machines revolutionized precision and automation in manufacturing, enabling the production of highly intricate and precise parts with minimal human intervention. CNC technology transformed the manufacturing industry, allowing for complex operations to be performed with unprecedented accuracy and consistency.
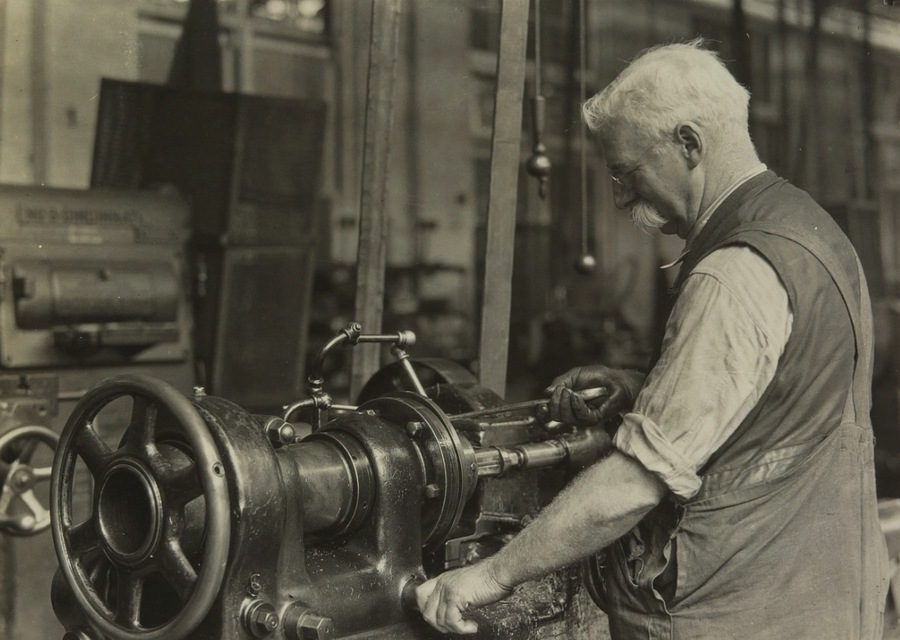
Types of Lathes
1. Spindle Machines: These versatile lathes are widely used for various turning operations. They have a spindle that holds and rotates the workpiece, making them suitable for general-purpose machining.
2. Precision Lathes: Designed for high-precision work, these lathes are used in applications requiring extreme accuracy, such as watchmaking and scientific instruments. They can produce very fine and detailed work, making them ideal for manufacturing delicate components.
3. Lathes and Rotary Machines: These combine turning operations with other machining processes, such as milling, to increase versatility and efficiency. By integrating multiple functions into a single machine, these lathes can perform complex tasks more efficiently.
4. Frontal (Lobotokar) Lathe: Used primarily for machining large, heavy workpieces that require facing operations. These lathes are designed to handle large-diameter parts, making them suitable for applications such as machining flanges and large gears.
5. Turret Lathes: These lathes have a turret tool holder that allows multiple cutting tools to be indexed and used sequentially, improving efficiency in repetitive tasks. Turret lathes are particularly useful in production environments where the same operations need to be performed on multiple workpieces.
6. Automatic Longitudinal Lathes: These are designed for high-volume production, automatically feeding and machining long workpieces with minimal manual intervention. They are commonly used in the manufacturing of parts such as shafts and rods, where high throughput and consistency are required.
7. Turning and Milling Machining Centers: These advanced machines combine turning and milling operations in one setup, allowing for complex parts to be machined in a single process. This integration reduces setup times and increases productivity by enabling multiple operations to be performed without moving the workpiece between different machines.
Importance of Lathes in Modern Industry
Lathes are indispensable in modern manufacturing. They are used in various industries, from utility services to aerospace engineering. The versatility of lathes allows for the creation and repair of shafts, pipes, bolts, and countless other components. Their ability to produce precise and consistent parts makes them a cornerstone of industrial production.
In the aerospace industry, for example, lathes are used to manufacture high-precision components such as turbine blades and engine parts. These parts must meet strict tolerances and quality standards to ensure the safety and performance of aircraft.
In the automotive industry, lathes are essential for producing parts such as crankshafts, camshafts, and brake discs. The precision and efficiency of lathes ensure that these components meet the required specifications for durability and performance.
Additionally, with advancements in CNC technology, lathes have become even more integral, offering higher precision, efficiency, and automation in manufacturing processes. CNC lathes allow for the production of complex and intricate parts with minimal human intervention, reducing the risk of errors and increasing productivity. The ability to program and automate machining processes has revolutionized manufacturing, making it possible to produce high-quality parts at a lower cost and with faster turnaround times.
Conclusion
Overall, lathes play a critical role in the manufacturing industry, enabling the production of a wide range of components that are essential for various applications. Their versatility, precision, and efficiency make them an indispensable tool in modern industrial processes.

I specialize in administrative technologies and am responsible for training other employees to use advanced systems and applications, including accounting software, mass communication procedures and organizational applications.